AC electric arc furnaces
General construction of arc furnaces
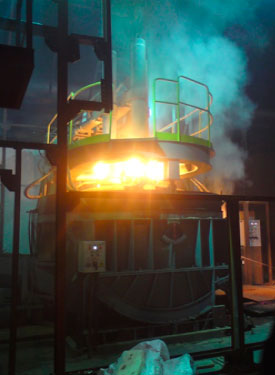
The main advantage of electric arc furnaces is the possibility of more successful, than in induction furnaces, carrying out of necessary metallurgical processes and, in particular, the removal of harmful impurities (phosphorus and sulfur) due to the high metal and slag temperature.
Arc furnaces constructions are divided into three types:
- furnaces of conventional design with mixture loading through a charging hole;
- runout-body furnaces with mixture loading through an open top of the furnace;
- furnaces with runout and rotating body.
Metal smelting runs in a furnace workspace, which consists of a bottom, walls and roof. They form the furnace lining.
Bottom and walls contact with liquid metal, perceive its weight at high temperatures, and are exposed to chemical reactions with the liquid metal and slag. Roof and walls appointment is to prevent heat dissipation. Therefore, the lining material may meet high requirements concerning fire resistance, durability and chemical resistance in accordance with an acidic or basic smelting process.
The most important parameters of the furnace workspace are bath depth, distance between roof and charging hole, and the electrodes circle diameter. When the bath depth is excessive the steel heating deteriorates, and the processes of interaction between steel and slag are slowing down. The bath depth depends on the steel composition and quality. It can be increased in case of carbon steel smelting and decreased in case of steel alloys smelting.
The deeper the bath, the greater the weight of steel, enclosing the furnace. The roof height over the bath has a very strong impact on the arc stability, it has to be selected sufficiently large. However, the high roof requires the significant length of electrodes, height of the furnace frames; external heat-transfer surface of the furnace increases, as well as the power consumption.
The electrodes circle diameter must be in a specific ratio to the furnace workspace diameter. If the electrodes are too close to the furnace walls, the walls lining will greatly deteriorate, which slow charge heating and melting in the central part of the furnace.
Too small electrodes circle diameter provokes worse heating near the walls and weaken the middle part of the roof, located between the electrode holes. The correct choice of the working space size is very important for the good furnace performance.
Arc furnaces lining
Refractory materials are characterized by the following features: refractoriness, Initial softening temperature under load, heat resistance, mechanical strength in compression, chemical composition, the ability to interact with basic and acidic slags, and cost.
Refractoriness is the property to withstand high temperatures without melting.
Initial softening temperature under load characterizes the temperature at which a sample of the refractory material 50 mm in height, which is under load of 2 kg / cm2 is compressed by an amount equal to 40% of the original sample length.
Temperature resistance - the ability to withstand sudden temperature changes without breaking: it is determined by the number of thermal cycles that fire bricks can withstand before they partly collapse and lose 20% of their initial weight. Thermal cycles are following: the bricks are heated to 850 ° C and then are rapidly cooled under running water.
In addition to high fire resistance not less important feature is the start of the softening temperature under load. In this regard obvious advantages have silica brick, despite their lower refractoriness. Particularly, this property is present in roofs, in furnaces with both acidic and a basic lining.
The most heat-resistant of the above refractories are chrome-magnesium ones, but they are very expensive. The greatest increase in size and volume upon heating have magnesite and silica bricks, but at high temperature magnesite bricks have additional shrinkage (1,0%), which leads to the formation of gaps between separate bricks. The increase in size is desirable in roofs and arches lining, as they increase the salience boom and lining strength, so magnesite bricks are not used for the roofs. In cases when an increase in the size of the lining has to be reduced, it should be put between the separate bricks easy-blow gaskets made of plywood, tar paper or cardboard. The roofs of magnesite and chrome-magnesium bricks should be winterized. The main property of insulating materials is low thermal conductivity, because the temperature on the inner and outer boundary layer reaches 1200-1300 °C. Just behind the high-refractory materials the chamotte bricks or lightweight bricks have to be located.
The most widely used binders are water glass and are fire clay, however, it is possible to use coal tar and sand.
Water glass is a technical sodium silicate soluble in water.
Refractory clay in dry form is used as a binder for quartz sand.
The process of melting in an arc furnace
Melting in the electric arc furnace is running under the influence of heat of the very powerful electric arc. High temperature in the furnace (near the arc - exceeding 5000 °C), together with the reducing atmosphere generated by combustion of electric arcs, allow production of steel alloys with such high-melting metals as tungsten and molybdenum, purify metal from the harmful and any impurities and melt steel with different amounts of various additives.
One ton of steel production in large electric furnaces needs 600-800 kW/h on average.
The electrodes energized via copper conductors. Arc furnace roof is suspended (it is attached to the portal with the help of chains).
When it is necessary to produce charge loading the roof is lifted and turned. Via overhead crane the bucket whose bottom consists of flexible sectors loads the charge materials into the furnace body. Then the roof turns and goes down onto the furnace. Electrodes are introduced through openings in the roof of and the melt begins. The arc lights between each electrode and the metal (the metal is a conductor), current flows from electrode to electrode through the metal. Electrodes are falling lower, and under each electrode there is gradually forming a lake of liquid metal.
Arc furnace is mobile, it can be rotated about a vertical axis in either direction, mixing the metal, reducing time for melting and downloading the slag. The furnace also rotates for the metal tapping to the ladle after its preparation.
In electric furnaces oxygen is used for process intensification.